Guided horizontal auger boring – Best installation method when installing gravity pipelines
Guided horizontal auger boring works perfectly in urban area and the method is cost-effective and thus widely used.
Together with the client from the beginning of the project
The best and most cost-effective situation is achieved when our equipment and services are brought in as early as possible, preferably already in the planning stage, by combining the input of consultants and planners. This way the possibilities of new technologies can be effectively utilized and cost savings gained at an early stage.
Guided horizontal auger boring at its best
Guided horizontal auger boring is a fantastic method, because by using the camera mounted to the machinery it is possible to monitor the position of the pilot pit’s centre point. If the pilot pit deviates from the route, it can easily be guided back to the correct route. Due to guidability the inclination of the drillrod may be changed during drilling.
Guided horizontal auger boring is very suitable for drilling in many different soil types and ideal for sand and clay.
Suitable for
- Installation of steel casing pipes
- Installation of concrete casing pipes
- Installation of composite casing pipes
– sewage and rainwater gravity pipelines
– pressure sewerline
– drums
– water pipes
– gas pipes - A very cost effective method in urban area.
- Can be used in many different soil types, ideal in solid sand- and clay.
- If necessary, can be used as an accessory to our horizontal auger boring machine when installing big diameter gravity pipes to desired tolerances.
Diameters and restrictions
- The installation conditions of the target (soil) must be carefully investigated before deciding to use guided horizontal auger boring
- Diameters from 160mm up to 2000mm
- Most typical boring lengths vary between 30-100 meters
- Method ideal for the installation when precision is paramount.
- Suitable soil: clay, silt and sand
- Problematic soil: blast stones, moraine and rock
- Pits and shafts: min. ø 2,5m

Methodology
Stage 1: Guided pilot drilling
Drilling machinery mounted in ø 2500mm shaft and installed in a desired inclination. Drillrod is being pushed with the drilling machinery and the inclination of the rod is monitored by a camera, which is directed to the centre point inside the drillrod. The inclination can be changed during drilling with the help of the steerable control head.
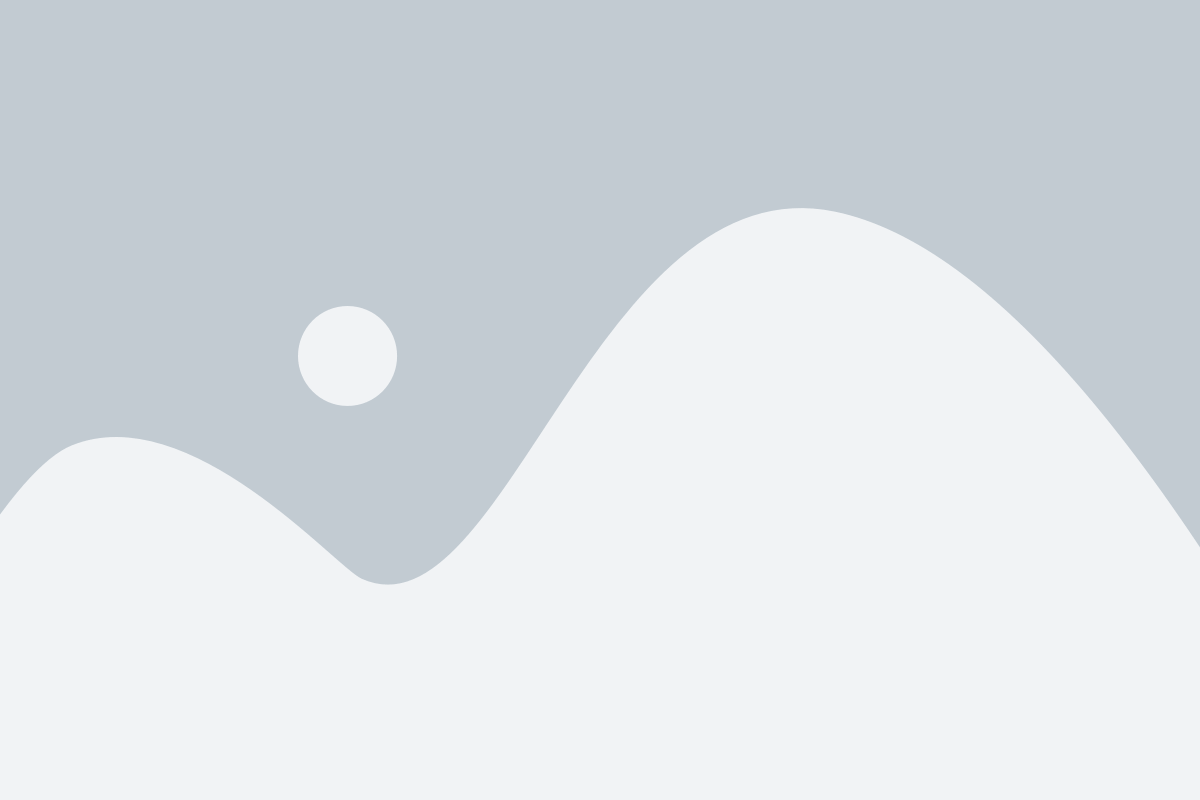
Stage 2: Augering
Pilot drilling is reamed to the planned diameter by using work pipes with augers inside. The work pipes are used to push pilot drillrods into the receiving pit.
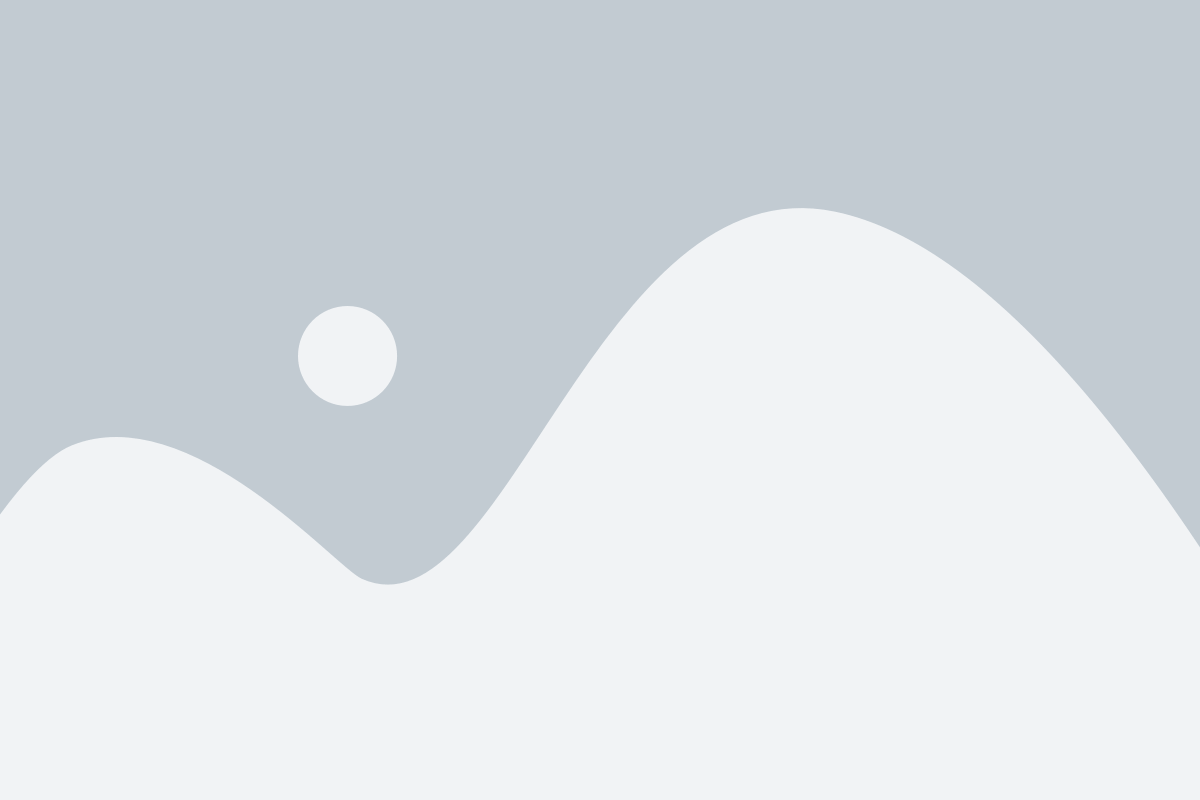
Stage 3: Replacing work pipes with final pipes
Work pipes are replaced with final casing pipes or flow pipes by pushing the work pipes out to the receiving pit.
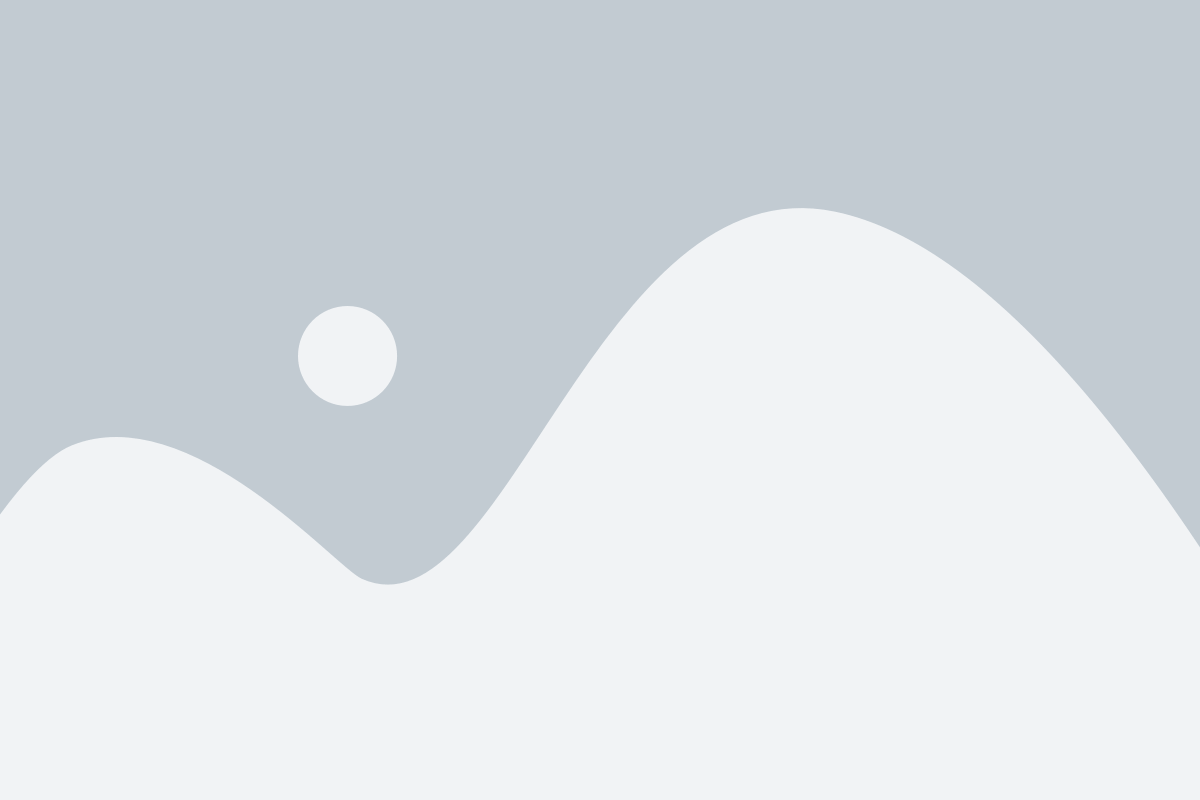